There are three genera of book printing technologies: letterpress, offset, and digital. Letterpress is now mostly a medium for artists and special editions. Offset and digital presses are both widely used to print books. This post is a look at how the unique characteristics of each offer different benefits to book publishers, and how new high-speed digital inkjet presses will change the book printing landscape.
Letterpress printing, which dates back to Gutenberg in the Western world, is still used by book artists for limited runs and was used for book printing (in the form of the Cameron Belt Press) as recently as the ’90s. Although it has been superseded by offset and digital for most book printing, we often produce books with letterpress-printed covers. The publisher supplies the covers, we print the interior and bind the book. Examples: Outer Pradesh, Psycho Dream Factory.
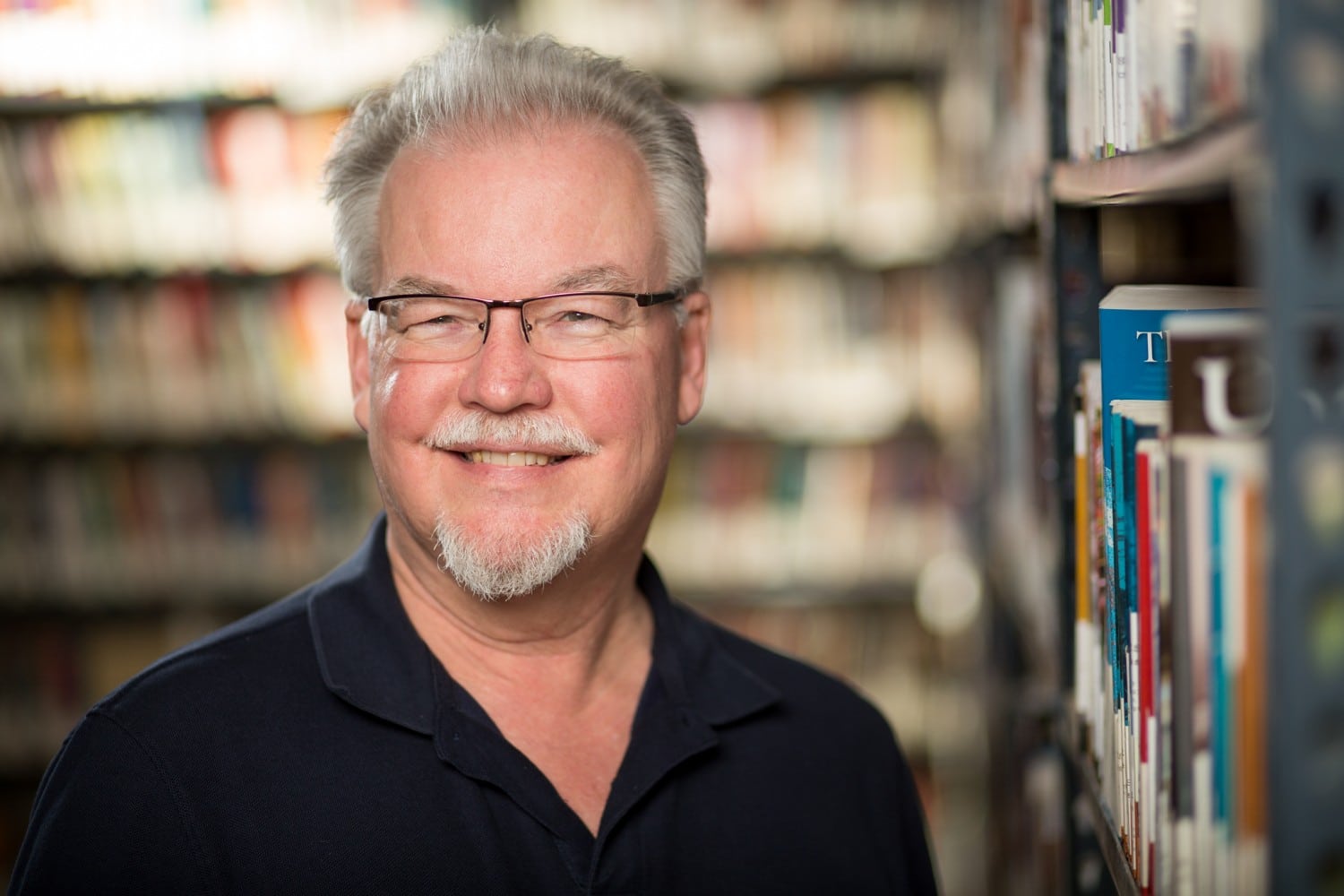
Don Leeper
Offset presses were developed in the early part of the 20th century. They became the predominant commercial printing technology in the 1950s. In terms of copies produced, the majority of books are currently printed on offset presses.
Digital printing technologies in the book industry date back only to the mid-1990s. Digital printing has been used primarily for short runs and Print-on-Demand (POD), but high-speed digital inkjet presses are projected to replace offset for all but very long runs.
Here, I will offer an overview of offset and digital printing technologies from the point of view of making books. Because of its niche status, I’ll leave letterpress for another post.
Offset Printing: How It Works
“Offset” is short for offset lithography. The “litho” in lithography is from the Greek lithos, meaning stone. Lithography was invented in Germany in 1796 by Alois Senefelder. Senefelder discovered that he could use fine-grained slabs of limestone, ground smooth, as printing plates. Senefelder’s process, like all subsequent variants of lithography, was based on the mutual repulsion of oil and water. Stone lithography uses the following steps to reproduce images:
- An oily material is used to create an image on the stone.
- The stone is moistened with water, which adheres to the non-image areas but not to the oily image areas.
- An inky roller is rolled across the stone. Ink sticks to the oily image areas but not to the water-moistened areas of the stone.
- Paper is pressed against the stone and the ink image transfers to the paper by contact.
Stone lithography is used to this day by artists to make prints, as the images it produces have their own unique aesthetic properties. As with letterpress, it seems that old graphic technologies never go away, but are instead repurposed by artists.
In offset lithography, the stone is replaced with a specially coated thin metal or plastic plate, as follows:
- Images of the book pages to be printed are created photographically or via laser scanning on the plate. The non-image areas are receptive to water, and the image areas are not.
- The plate is mounted on the plate cylinder of a press.
- As the plate cylinder rotates, a film of water is applied to the plate from a fountain on the press. Water adheres only to the non-image areas.
- A roller applies oil-based ink to the plate as the cylinder rotates. The ink does not stick to the areas of the plate moistened with water, but does stick to the image areas.
- The rotating plate cylinder presses against a rotating offset cylinder, transferring the ink image from the plate to the rubber-coated surface of the offset cylinder.
- The rotating offset cylinder then transfers the ink image to paper being fed through the press.
In offset book printing, multiple pages are printed simultaneously on each side of the large sheet or wide roll of paper. The paper is then folded after coming off the press into signatures of 8, 16, 32 or 64 book pages. The folded signatures are then gathered together in sequence into a book block. During the binding process the cover is attached to the book block by using glue and in some cases thread.
Offset printing is capable of very high speeds and very high quality. While the platemaking and press setup is time-consuming and costly, once a press is up to speed, sheets can be printed extremely cost-effectively at rates up to 15,000 large sheets per hour. The same is true of long-run binding machines: they require a long setup time, but offer very fast production when they are up and running. Because of the platemaking, press makeready, folding, and gathering processes required before a single book is actually produced, in general offset printing is not efficient for runs of less than 1,000 copies. Offset book printers are quoting runs as low as 500 copies in order to hold onto customers who are requesting shorter and shorter runs. Fast makeready offset presses like the Variquik and the Timsons have also helped to increase efficiency at lower quantities.
Digital Printing: How It Works
The digital printing process skips over many of the steps required by offset printing. Here’s a typical imaging path:
- A rotating imaging cylinder has an electrostatic charge applied to its specially treated surface.
- A laser (or LED) scans an image onto the cylinder: the laser light removes the previously set charge from just the image areas of the cylinder surface.
- The imaging cylinder rotates past a reservoir of very fine electrically-charged toner particles, which leap across space to stick to the oppositely-charged image areas of the cylinder. (It is essentially the same process as when static electricity attracts dust to a surface, but finely controlled.)
- The imaging cylinder transfers the image to an oppositely-charged transfer belt (or cylinder).
- The transfer belt then transfers the image to paper moving through the printer.
- The toner particles are fixed on the paper with pressure and heat.
Toner-based digital printing processes are capable of speeds up to about 200 feet per minute on rollfed presses. Sheetfed toner-based presses can print up to about 150 impressions per minute, or 300 impressions per minute on presses that print both sides of the paper at the same time. The best machines offer quality comparable to offset for both type and images. The key advantage of digital over offset is that it uses no expensive plates and there is minimal press makeready time. Also, the process creates a new print image for each revolution of the imaging cylinder, which means that complete page sets come off the end of the printer–no folding or gathering is required after printing. The book blocks are ready to bind with minimal preparation. The tradeoff is running efficiency: while much less costly to set up a job, the cost of running the job is more than offset, because toner-based printers require constant maintenance to run large volumes. Because the process is based on creating dueling electrical charges, fine powders, and the application of heat, it is extremely finicky and subject to disruption by ambient temperature and humidity changes, paper quality, and other issues. The maintenance, aka “click charges,” is billed to the operator of the press by the manufacturer based on how many pages are printed. These click charges can exceed the cost of the paper being used. Despite all this, toner-based digital presses have become very technologically advanced and have enabled the production of very useful, high-quality, short- and medium-length press runs.
In general, for 1,000 copies or fewer, digital book printing has a cost advantage, and at 2,000 copies and above, offset printing has the advantage. Between 1,000 and 2,000 the advantage can go either way: digital or offset may be cheaper, depending on factors like page count and binding type. Sometimes schedule is the tie breaker: a rush digital print run only takes a few days, whereas a rush offset run is more likely to take a few weeks. We have printed as many as 6,000 copies for a run of a book where the author won the Nobel prize and the publisher was hot to get more inventory into sales channels. Also, offset still has a 500-copy floor for reprints, whereas it is quite practical to order a reprint of 50 copies or fewer from a digital book printer.
The Inkjet Promise
New high-speed inkjet digital presses coming onto the market may eventually offer the best of both worlds: the low setup costs of digital presses and the operating economies of offset presses. Inkjet presses are ginormous siblings of the inkjet printer you may have on your desk for printing letters or photos. The typical inkjet press is about 50 feet long, weighs several tons, and prints on a roll of paper moving through the press at 400-650 feet per minute. Arrays of superfine nozzles shoot microscopic droplets of special ink at the moving paper to create the page images. As with toner-based digital presses, and unlike most offset presses, pages for an entire book can be printed in one pass, meaning that book blocks can come off the end of the press ready to bind. (As a practical matter in most installations the printed roll is actually taken off the press and sliced and diced into pages on a separate machine.) Also, the press need not stop or slow down to start printing a completely different book, as long as it is being printed on the same paper.
Currently, high speed inkjets cannot match the quality of either toner-based presses or offset presses, but companies like Canon, Ricoh, and Kodak are investing tens of millions of dollars in research and development to drive inkjet press technology up the quality curve. High-speed inkjet presses now currently find the most use in the education market, where reproduction quality requirements are lower than books sold in the book trade.
In addition to the rollfed inkjet presses, manufacturers are also developing sheetfed inkjet presses. As with offset presses, digital presses that print on sheets are slower than those that print on rolls of paper, but printing quality is higher because a sheet can be much more precisely registered to the plate, transfer cylinder, or inkjet heads.
As inkjet press quality improves, it is almost certain to replace offset presses for many medium-run printing applications. A signal of this trend was evident in the exhibits at the 2014 Graph Expo printing trade show, which was dominated by digital press companies Ricoh, Xerox, HP, and Kodak, while old-line offset press manufacturers like Heidelberg and Komori were either absent or almost invisible.
Bookmobile’s Take on Inkjet
Here at Bookmobile we have been watching inkjet press development for several years. Our operations manager Dieter Slezak and I have visited the Kodak plant in Dayton twice, the Ricoh plant in Boulder several times, and inspected HP, Canon and Xerox inkjet presses at trade shows. With each iteration there have been improvements in the technology, but inkjet still lags toner-based presses significantly in terms of what paper you can print on and the reproduction quality of type and images. While operating cost of inkjet presses is supposed to be lower than toner-based presses, and inkjet presses are faster, the cost of the least expensive inkjet is five times the cost of a toner-based press. With that in mind we opted not to go with inkjet when we replaced our six black-and-white digital presses early this year. Instead we acquired four Océ 6320 black-and-white sheetfed presses, adding rollfeeders to three of them. Based on extensive print samples and running the numbers, this was clearly the optimum choice in terms of keeping prices low and quality high for our customers. On the quality side, I do not see inkjet ever surpassing the Océs for monochrome printing.
For color printing, we are waiting for inkjet to match or exceed the quality of our toner-based color presses. The inkjet press manufacturers have some serious challenges in enabling high-quality color printing on both coated and uncoated paper stocks that aren’t super expensive. Also, the presses themselves cost several million dollars. Capital cost of these presses needs to come down and quality needs to come up. We think the manufacturers will achieve this, probably in two to four years: the recently announced Canon Niagara sheetfed inkjet press looks like progress. When inkjet presses enable us to offer high print quality and better prices than we can now, we will move.
In general, there is no question that digital printing technologies will continue to transform book printing, replacing offset for all but the longest runs and offering publishers new flexibility in managing print inventory in a way that minimizes risk, keeps overall costs down, and maintains quality.
Need a quote or more information?
I’d be happy to answer questions. Contact me via email.
You can request a printing quote or ARP proposal here.